Major Engine Update:Changing the Crankshaft Oiling System Porn, uhh . . . . . photos . . . . . (I tried to get Stormy Daniels to hold the pointer in the photos, but, as luck would have it, she's busy . . .)SO, I get asked: "Why are you doing this? You think you are smarter than the guys (sic, engineers) who made (sic, designed) the engine?"
Buzz and I only need one bullet point to answer this question . . . . . .
A/ YES.
The problem, as I see it:A/ This engine was designed as a "grocery getter", not with high rpm "performance potential" in mind. (More or less direct quote from the primary engine designer.)
2/ Within the "performance engines" based off this unique design and using the standard oiling system, higher than normal rod bearing wear, at high rpm, is well known,
and accepted.d/ Servicing, ie, replacing worn rod bearings, although a simple procedure on conventionally designed engines, on this unique design, results in a major disassembly of the engine.
SO, knowing this, the decision that has to be made is:Am I willing to accept lowered performance, compromise engine longevity and possibly risk catastrophic failure to an expensive engine that can not be easily repaired or replaced?
With knowing those factors and placing the question into that context, it becomes an easy answer . . . . .
A/ NO!!
And Chris agreed, since it was his wallet that was going to take the hit.
So, what is it going to take to resolve this potential problem? Both design-wise, AND, cost-wise . . . A/ Well, the crank oiling passages needed to be revised. But since it needed a special de-stroked billet crank, revising the oil drillings was not an issue. Additional cost $0.00
2/ The main bearings on main journals #1 & #5 need to be revised to permit oil feed to their adjacent connecting rods. This was an easy solution as the requisite bearing already existed. The main bearings for journals #1 & #5 were originally BOTH plain, ungrooved shells, as they only oiled the main journal. BUT, the main journal bearings for journals #2, #3 and #4, since they oiled the connecting rods normally, used the conventional bearing construction. A plain ungrooved shell on bottom, with a grooved shell on the upper. This represents the best compromise of load carrying and oil supply. So additional grooved bearings were needed to be added to the #1 and #5 positions. Fortunately, Mahle Motorsports produces a competition quality main bearing set in Vandervell VP2 material. (Produced in the original Vandervell factory, as I understand it.) But, they are supplied for the standard oil system of 3 grooved shells and 7 plain. So the additional cost is the price of a second set of competition grade main bearings approximately $125.00 And this allows us to "steal" 2 more grooved bearings for the re-designed system.
d/ Since the different bearings have different tangs, (so they can't be mistakenly switched), the block would need some fairly trick machine work to revise the bearing tang notches. Additional cost ? ? ? ? ? ?
So that's how we got to here, and the photos are below. But first this:
We are publishing this for a variety of reasons:A/ Chris has always intended this "Build Diary" to be a complete compendium of his journey. Warts and all. Flatlanders included. And I agree with all. Except the cats . . . . . . .
2/ It is an example of how engineering experience can avoid potential problems using good judgment. Readers should apply this judgment and logic to their own builds.
d/ This post is intended to provide a "blueprint" for a way forward, to those racing these K series engines, and experiencing this problem.
And now, the porn . . . . uhhh . . photos . . .So here is the problem . . . . . #1 journal
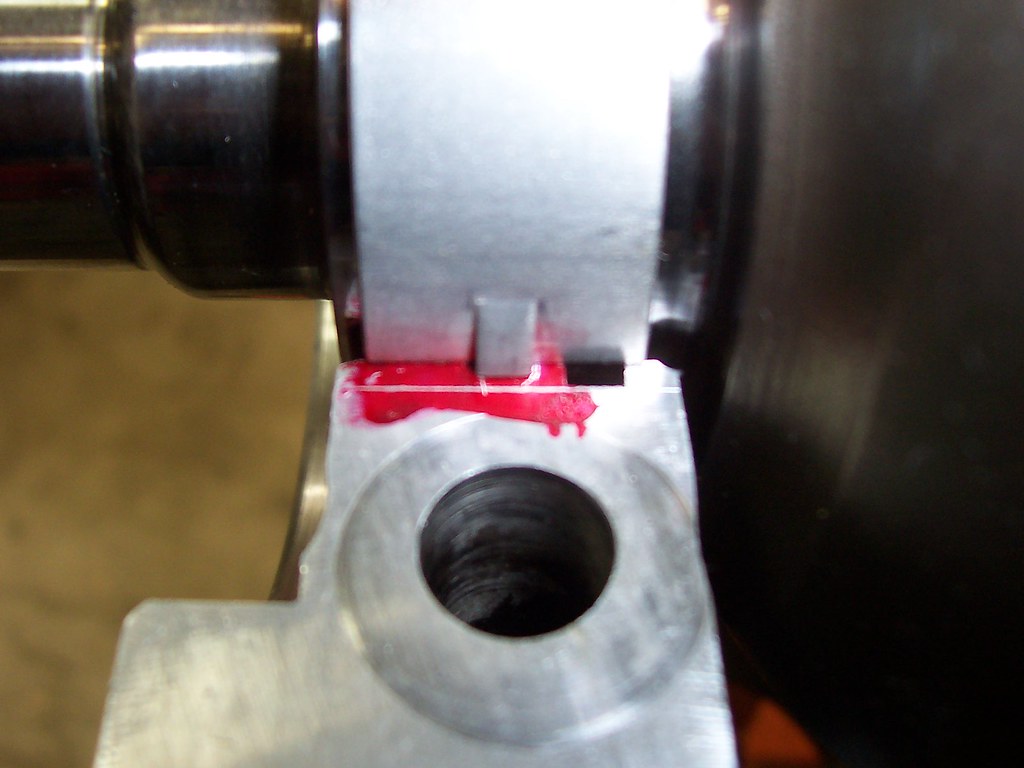
Same problem, #5 journal . . . . .
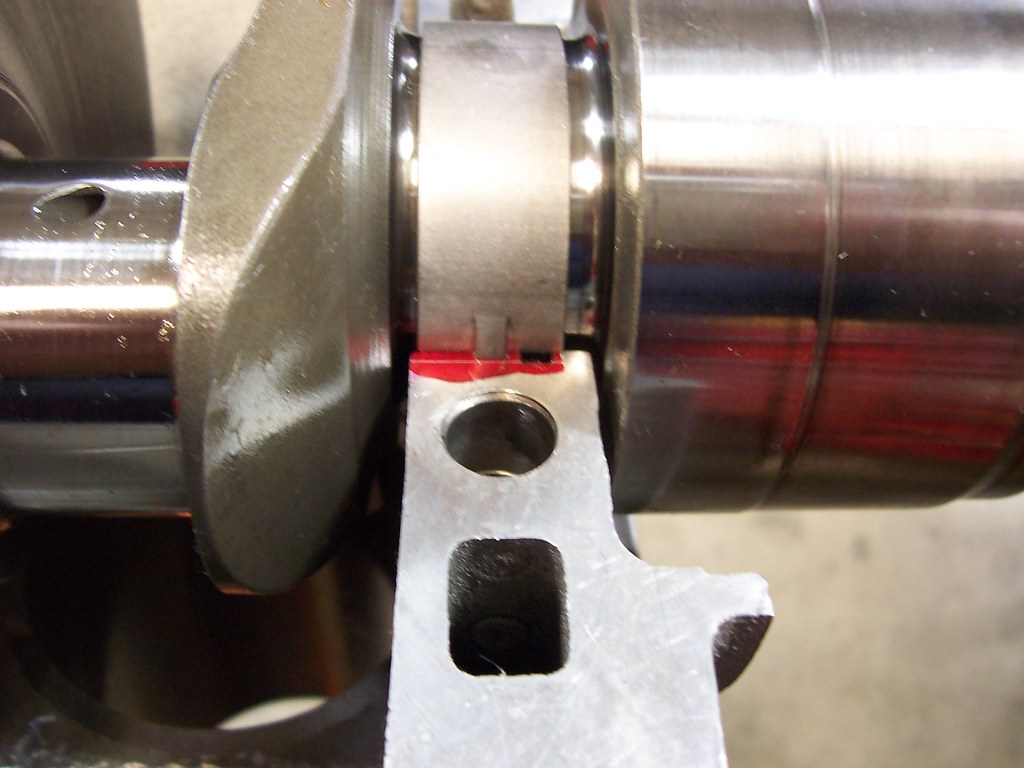
The setup for the "correction" on #1 journal . . . . .
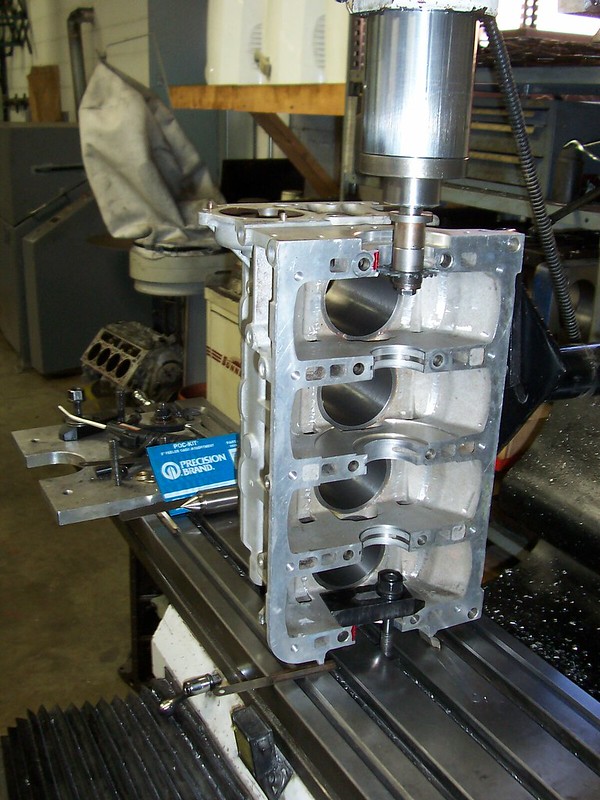
And, of course, the block faces are not "flat" . . . . .
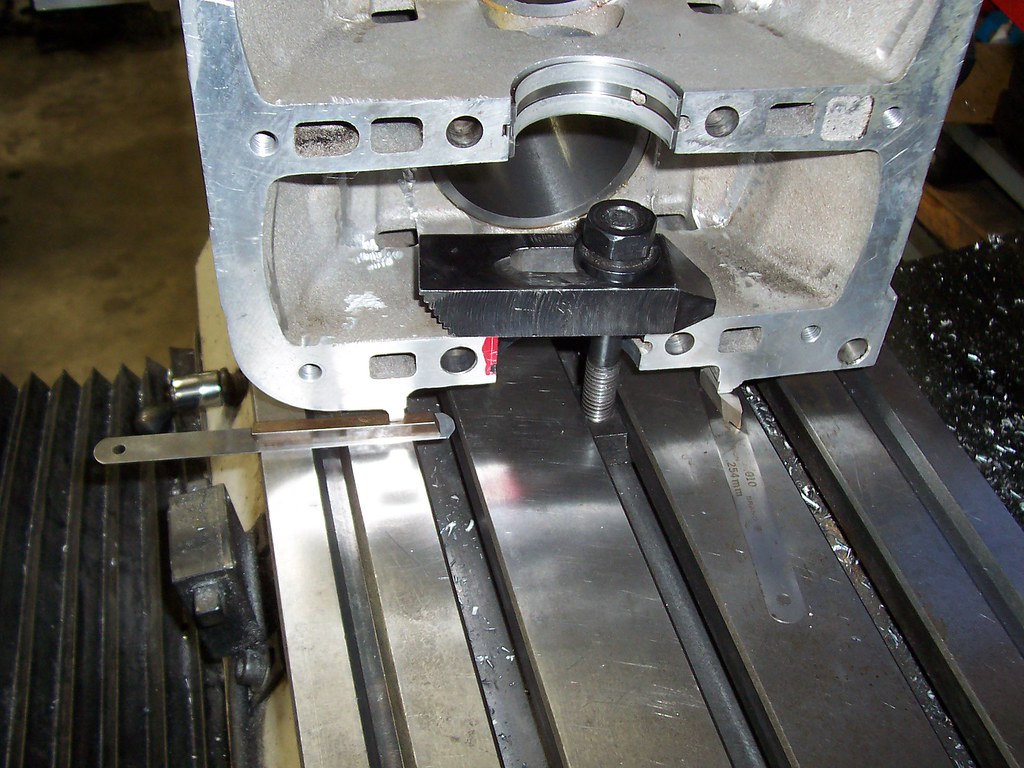
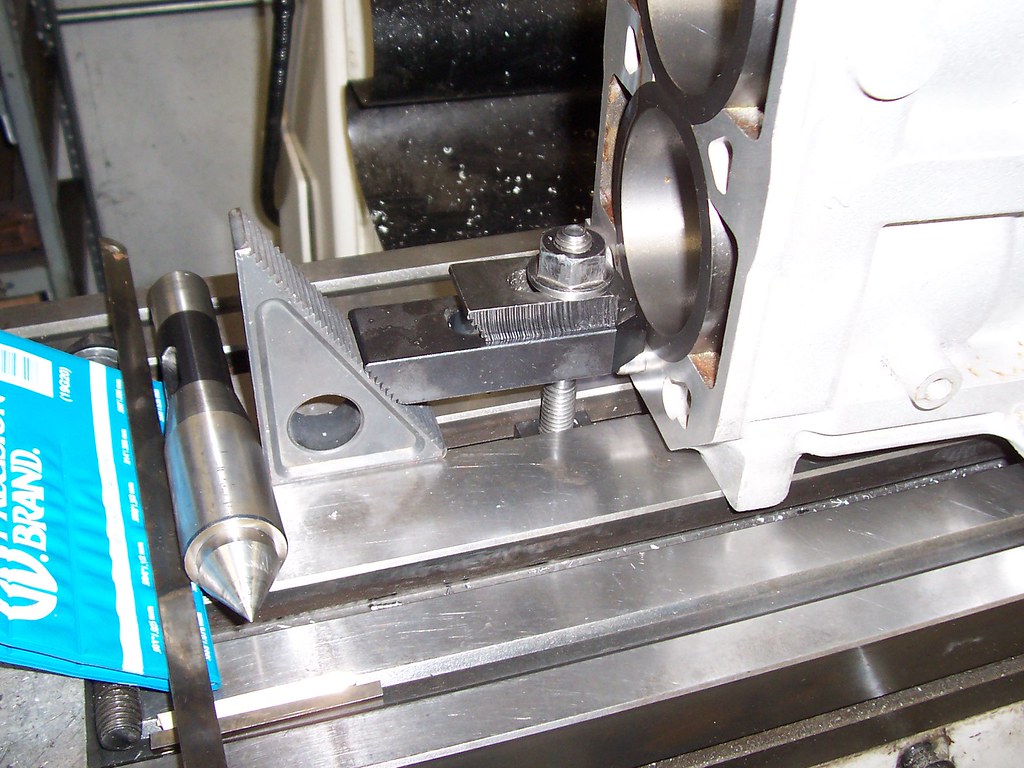
And the finish . . . . .
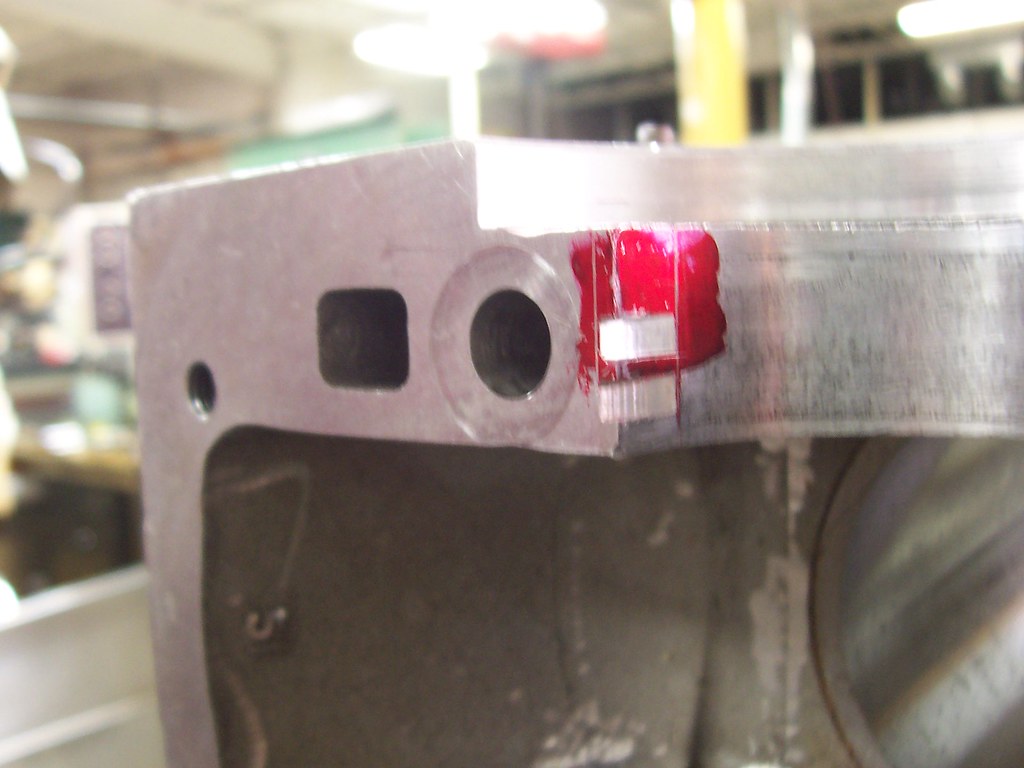
Grooved bearing fitted . . . . .
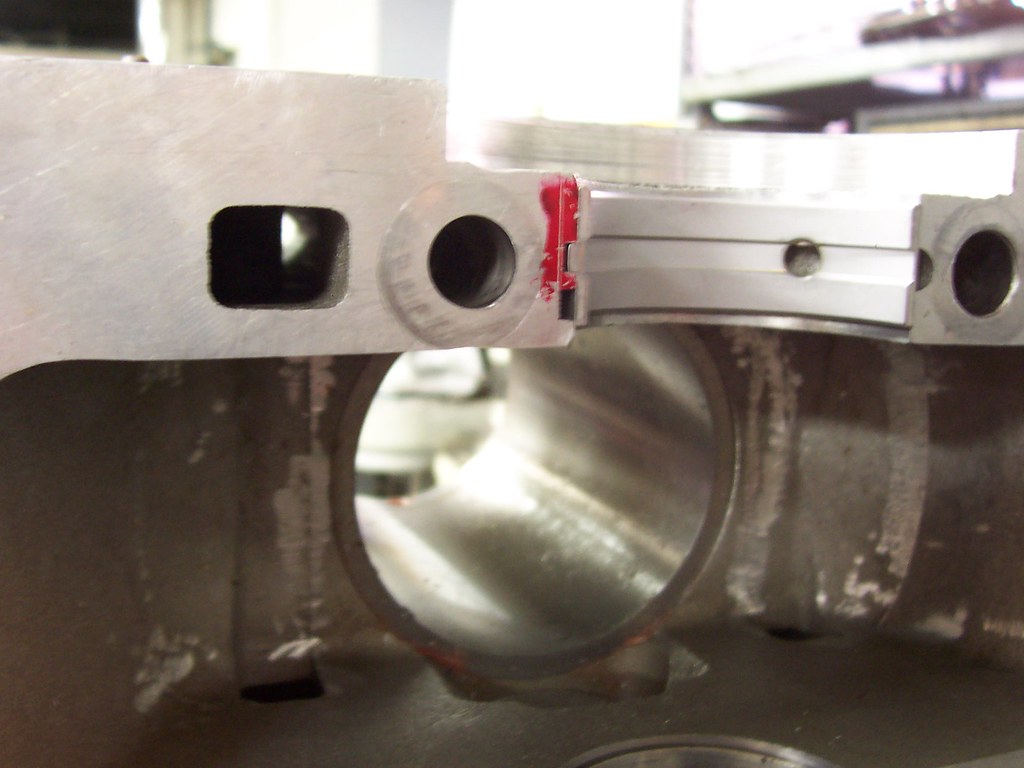
Repeat for the #5 journal . . . . . .
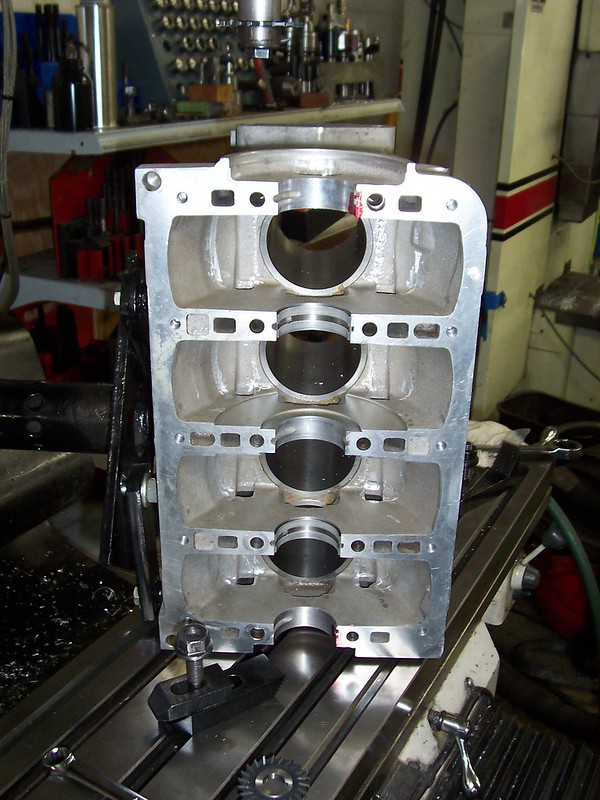
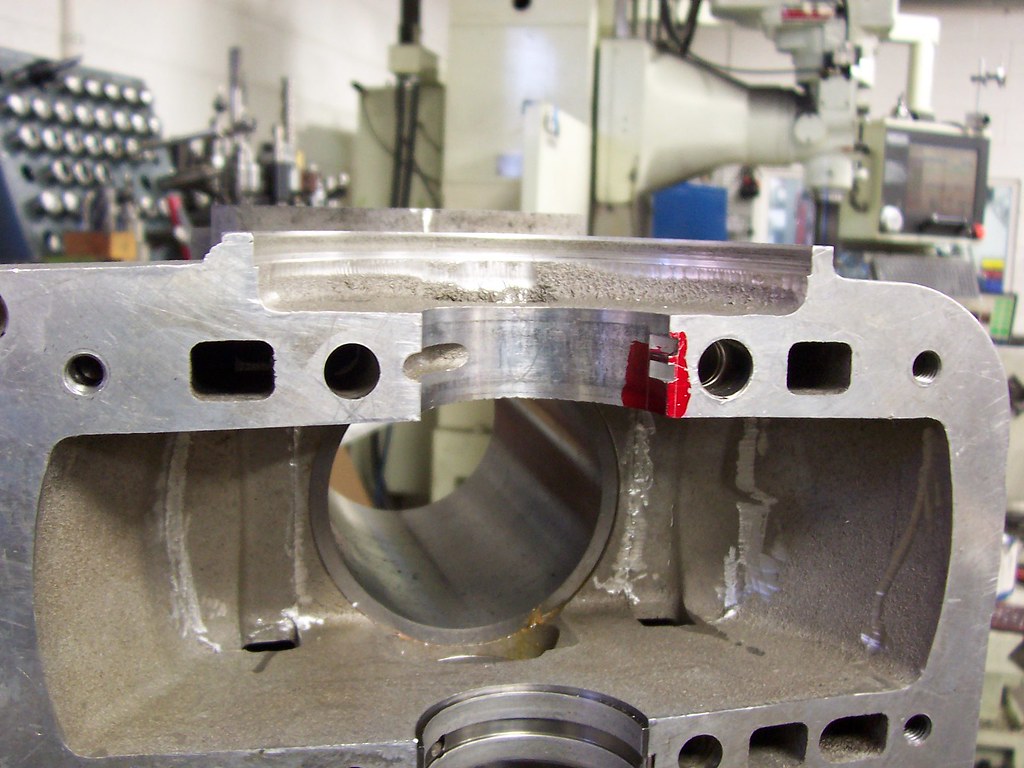
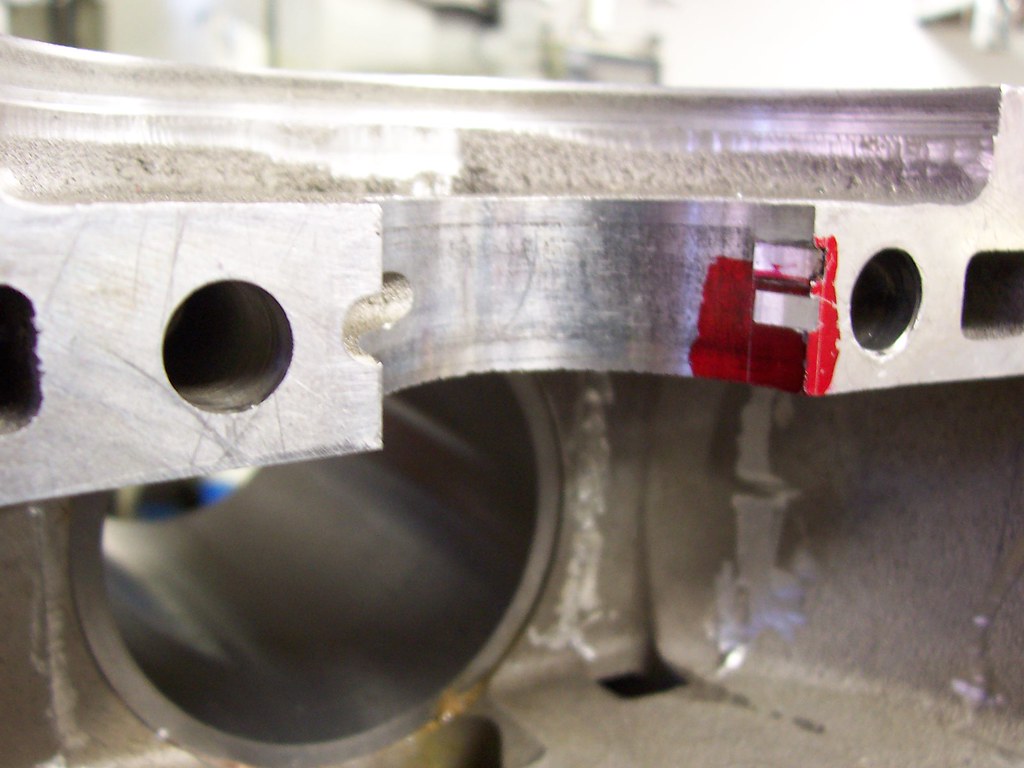
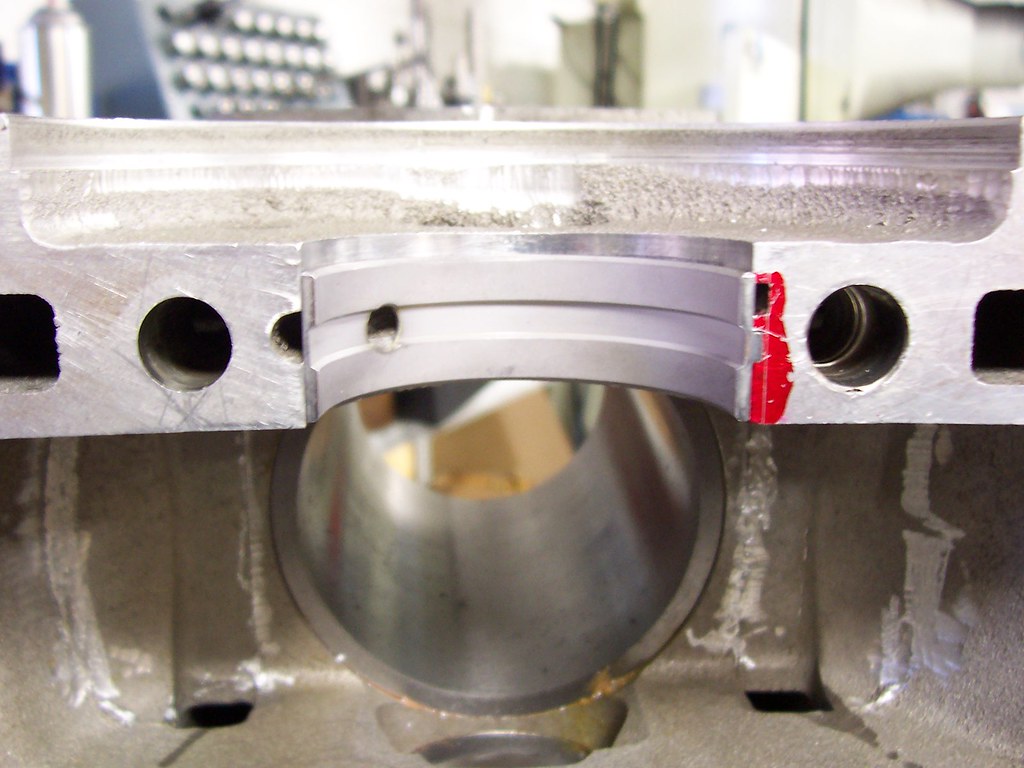
And before anyone asks, YES, the bearings were slightly shifted longitudinally. This was done to retain as much material as possible between the original bearing tang notches and the new notches. I wanted to avoid welding up the old notches and "creating" more machine work. This "shift" needs to be done carefully, so the bearing chamfer doesn't interfere with the crankshaft journal radius.
I'll post the results of this operation later in the day.
For now, I'm asking for feedback from any reader who is racing a K type engine and having bearing problems. I know you are out there lurking, sign up and post a comment.

Machinistboy