.....
OK, a clarification of a couple of things...................................
You mean; a LOT of things.
Fantastic !
...I'll go through it all later today when I've picked up a new bottle og argon,
and have time to run some welding tests.
Thanks Whizz !
BTW ; guess we must have ran into one an-others frame of vision
at BUB back in 2008.
I took some pictures of your bike ( and you, I guess) :

350 Triumph engine..right ?
Hope to see you there this year.
The Arc Force knob is used mainly when stick welding .......
OK thanks. I'll probably be back with more questions on stick welding
when I get around to trying that feature.
I mentioned above, this place with which I cooperate,
that do "big" alu-stuff.
Right now they a building a 12 meter ( close to 40 feet) -diameter "globe"
made of circles that together form a 'grid'-globe.
Inside this sits a smaller 'globe', and inside that sits a stage
for sword fighting. It's for an outdoor theater play
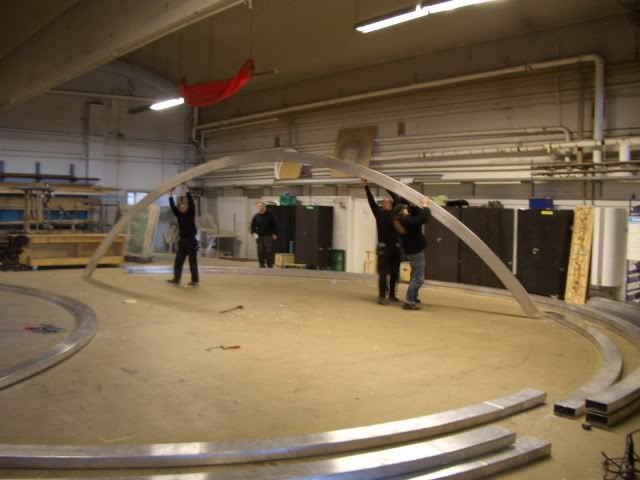
They have a real nice selection of materials, from which they let me pick what I need. ( This is just part of it)
Nice!
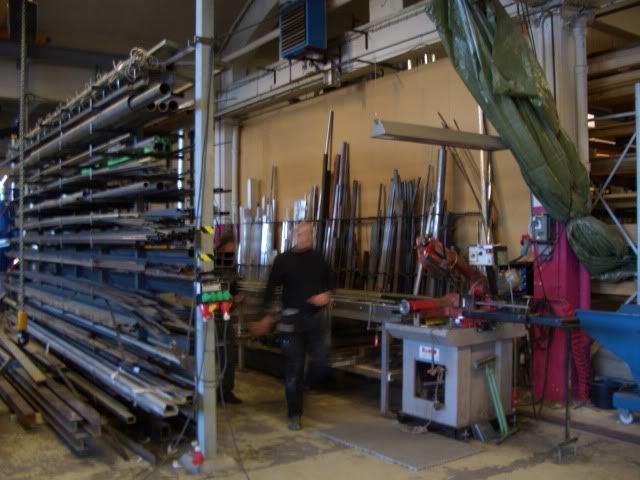