The head came back today after a .060 haircut. The head skim was a bit harrowing. When you slice cheese this thin, you sometimes discover Swiss cheese

Its just the water jacket on the face, which both Mel and Fordboy agree should not be an issue. A dab of HT silicone against the face and against the gasket should keep it from leaking, but this is an indication of just how extreme this combination is being stretched. Part of the issue is the lack of cylinder capacity with respect to chamber capacity. In order to get a CR that will produce power, the chamber needs to be as small as possible, so pushing things to the limit and in this case, a tad beyond - is what needed to be done.
Ill be scrubbing up the castings this evening, and next week, Ill meet up with Fordboy, he'll cc the chambers and well see what out final CR is going to clock in at.
Midget, et all,
Completely ignoring the risk to self brought about by a foray into the Land of Lincoln whilst driving a cheddar plated vehicle, Chris appeared on the doorstep of the ranch/dungeon with the 'Swiss cheese' (cylinder) head. Got out the trusty burette for the cc'ing process to determine final static compression ratio. Followers of Midget's diary may recall that the original static c/r was
10.48/1 when the #1 combustion chamber measured out @ 22.5 cc's. Not quite enough for full race. Some specification changes were proposed, with the goal being to achieve as close to 14/1 static c/r as possible, given the physical limitations of the bits.
Post machine shop haircut, the head measured out at:
#1 17.3 cc's
#2 17.2 cc's
#3 17.4 cc's
#4 17.3 cc's for an average of 17.3 cc's per combustion chamber.
Anytime the tolerance is +/- .1 cc ALL of the machine work has been very well done. The valve heights are very even, denoting attention to detail in the valve & seat work. And the chamber heights are even as well, meaning that attention & precision were in evidence for the milling/skimming process as well. Kudos to all whose hands massaged this head. The calculation on skimming the head .060" was for a minimum 4.5 cc to 5.0 cc volume reduction. A 5.2 cc reduction was achieved due to the chamber edges being angled outward to improve flow, which gives an irregular volume/shape ratio.
Combining the reduction in head cc's with the block milling (piston height going from -.004" to +.008", which will be confirmed on build-up) the resulting static compression ratio works out to be:
13.56/1, which given the resultant 'Swiss cheesyness' (

) of the casting, is the limit of what can be achieved with this particular head casting.
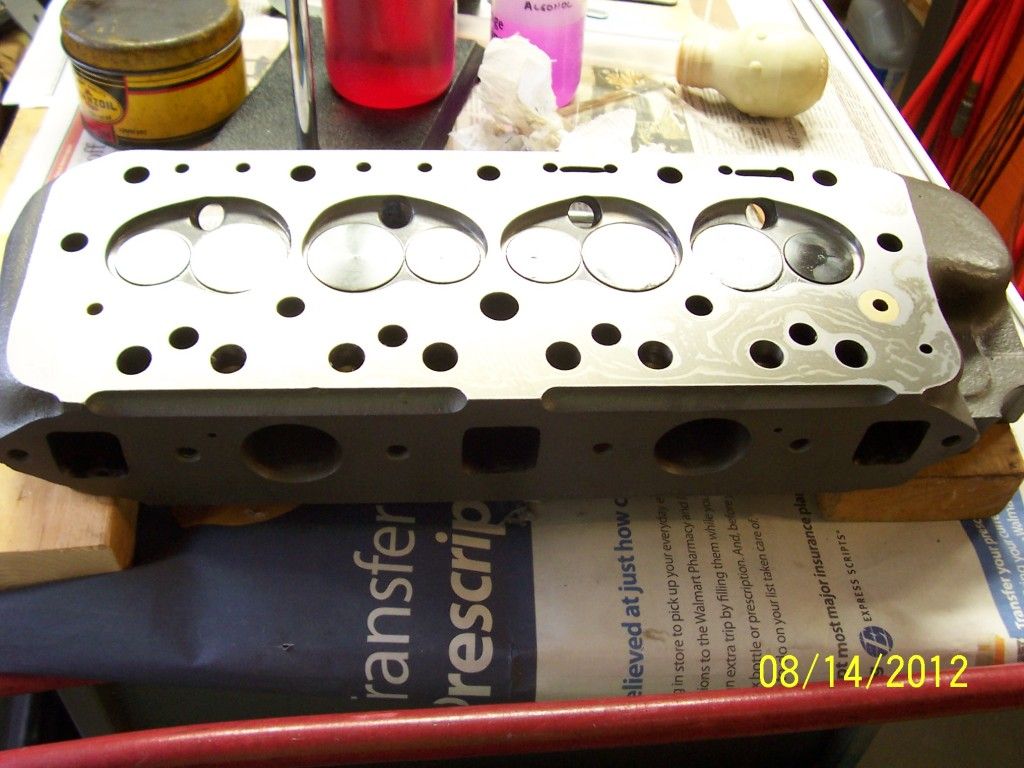
Standby for the 'Frankenstein mods' to the cylinder block, in the next post.

FrankenFordboy