Aha!

One step backwards and one forward. Last night when I was assembling the engine core I managed to turn the thrust bearing the wrong way and before I noticed it the thin cast alloy wall that holds the thrust washer cracked.....
Breaking the cast diffuser plate with countless of hours of work put into it was no fun feeling, I had to sit down and consider my options for a while before I came up with a solution. It never occurred to me to take any pics of the damage, I had other things on my mind.
Since that thin wall was the only thing acting against the axial thrust it might have failed sooner or later anyway, so I decided to remove the damaged wall and turn a recess into which a stainless wall can be fitted.
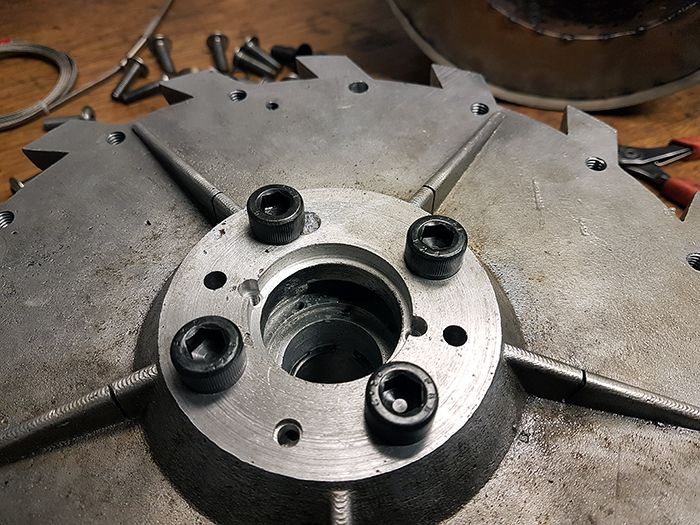
Here I have started making the stainless part, I have milled and threaded two M4 holes to secure it.
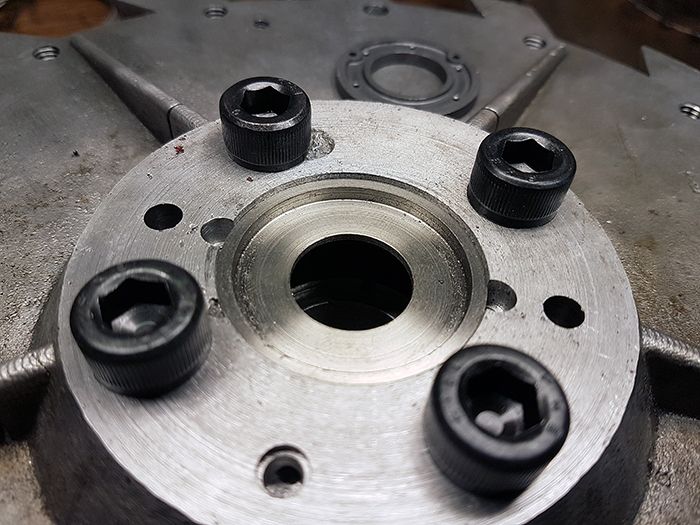
The thrust washer is dropped in place just for reference.
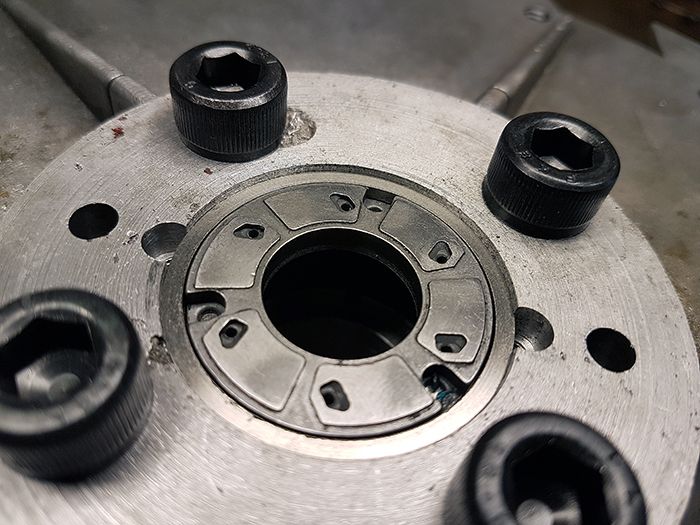
A pair of matching recesses were milled in the part for the M4 screws, now it can´t go anywhere. After the pic was taken I drilled the three 3mm holes for the thrust washer so everything could be screwed together.
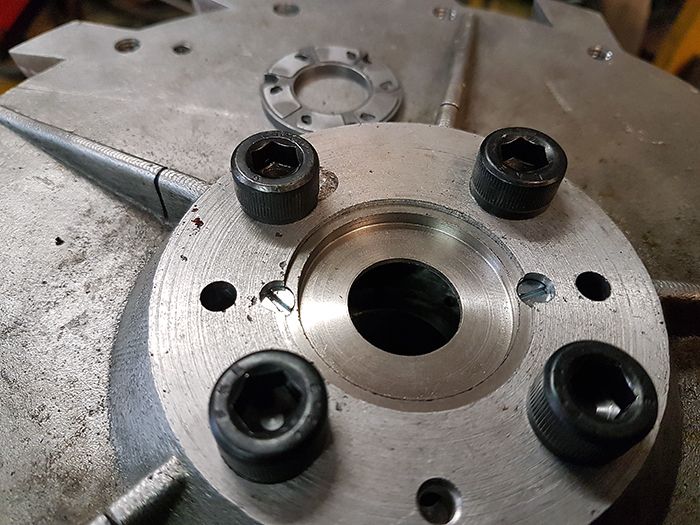
I took .05mm cuts from the stainless wall until the end to end axial bearing clearance was 0.20mm, well within specs but on the sloppy side in case something tightens up when the engine heats up. Now I just have to mill the oil ports that lets oil in from the backside of the wall to the thrust washer, then I can continue assembling the engine.
The best thing about this is that the axial clearance is set by removable parts and not the diffuser plate itself, so any modifications in the future can be done to these small parts without risking any damage to the cast part.
Pheww.
