This weekend the rest of the family are away, so I have three whole days for myself. A strange feeling for someone with small kids, I spent the whole day in the workshop and got a fair bit of work done.
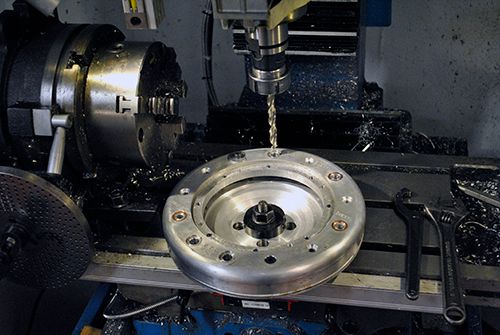
I made the oil pressure tube that goes through the compressor housing and an AN6 fitting that is threaded to fit the tube.
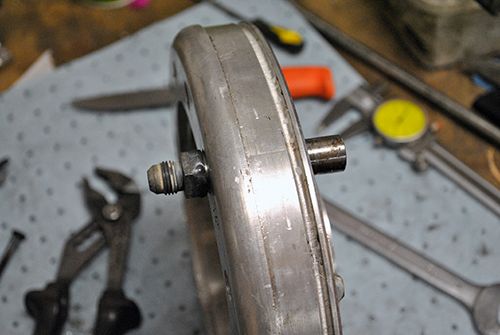
A bit more work on the mill and lathe and the oil pressure tube is ready to have the internal oil line welded to it.
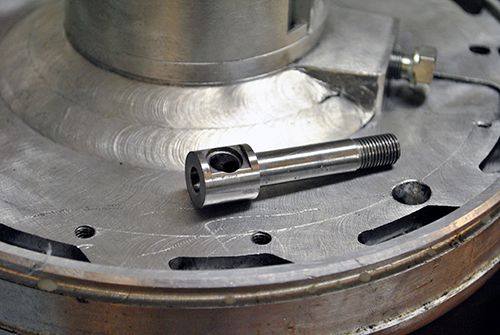
Everything set for tig welding!
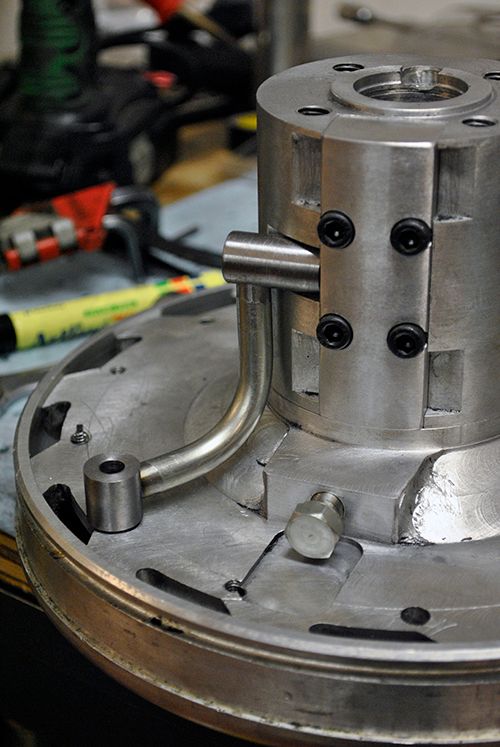
The oil line is cooling down after welding.
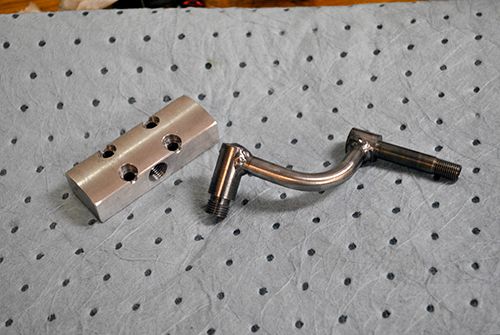
With that done I milled O-ring seats in the distribution block, the silicone rings were bought on Ebay for 1/20 of what a local dealer would charge me...
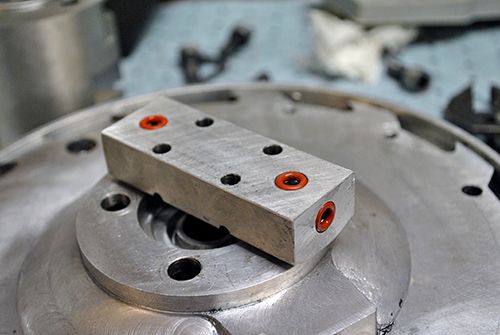
The insex heads were drilled for lock wire, don´t want them to come loose and drop into the turbine wheel.
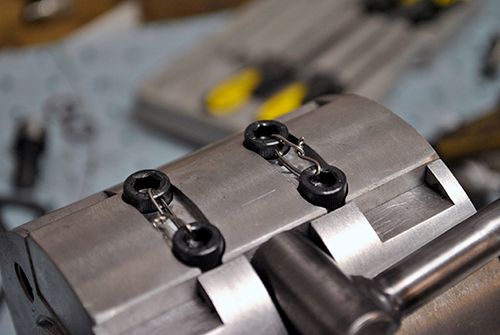
Now it was time to fix the oil leak in the compressor housing, a piston ring seal on the turbine shaft is meant to hold the oil inside the shaft tunnel but during the mishap last winter when the compressor wheel came loose the piston ring sealing surface in the aluminum housing was damaged and started to leak oil.
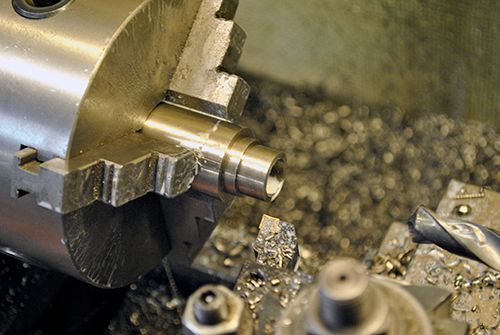
I made a bushing in stainless that the rings will seal against, another benefit with this is that I could make it long enough for both piston rings. Earlier I could only use one ring due to space restraints.
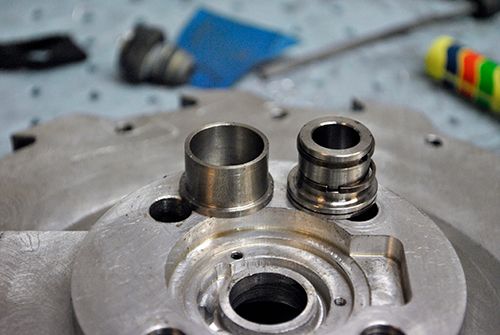
I opened up the hole in the compressor housing so the stainless bushing could be pressed in place.
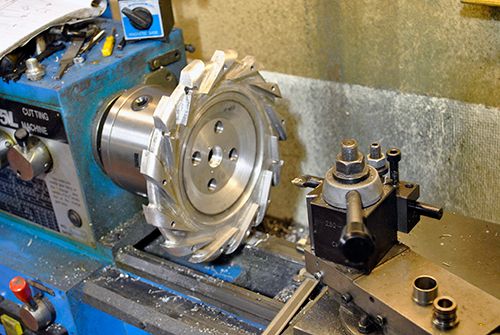
To make sure it wouldn´t spin or drop out I milled two recesses in the compressor housing and grinded two slots in the stainless bushing, a pair of punch marks locked it firmly in place.
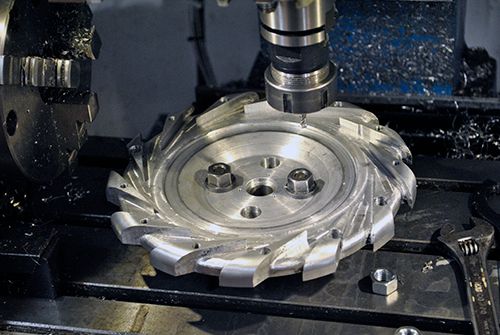
Like this.
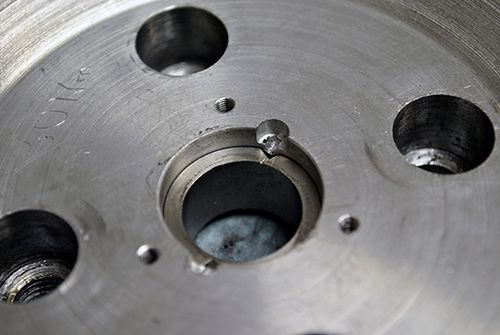
The oil hole for the thrust bearing was then drilled, very important that it is perfectly centered against the O-ring to avoid oil leaks.
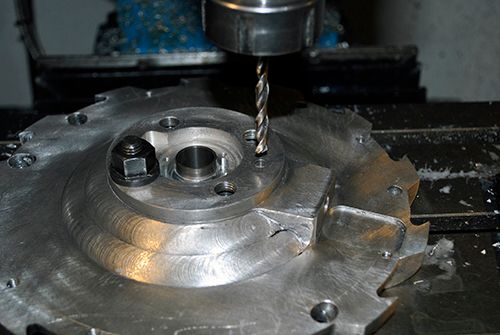
Finally I could start to assemble the engine again, you can see a plug fitted where the old banjo oil fitting used to be.
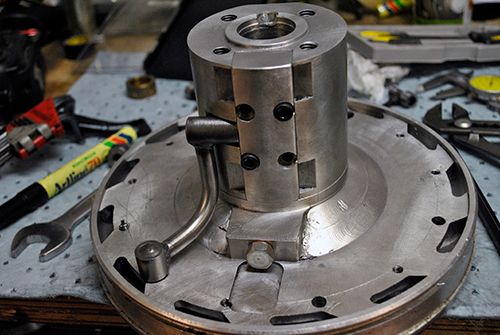
Bearings and oil scavenge line fitted, by now I was pretty hungry so I called it a night and went inside to try to find me something to eat.
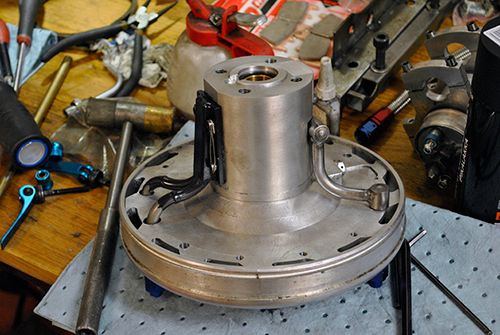
Cheers!
/Anders