While waiting for some parts for the turbofan build I continue with the JU-02 project, the time has come to construct the test rig!
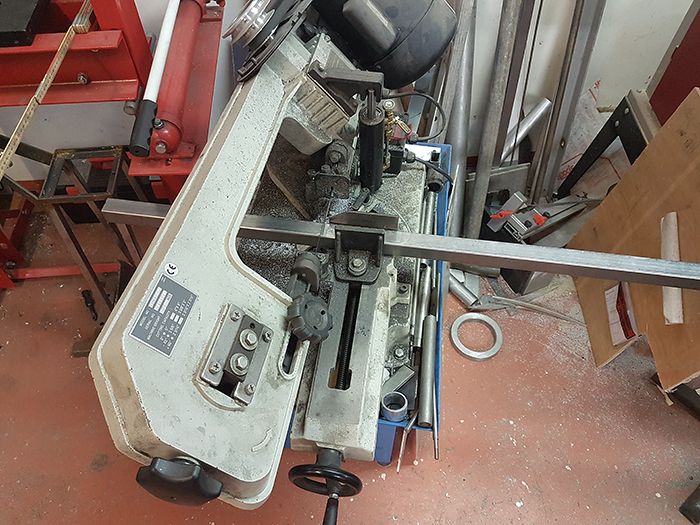
This time I plan to use a load cell to measure the thrust correctly, the "frame tubes" onto which the engine will be clamped have a sliding fit in the test rig so they can transfer the thrust to the load cell.
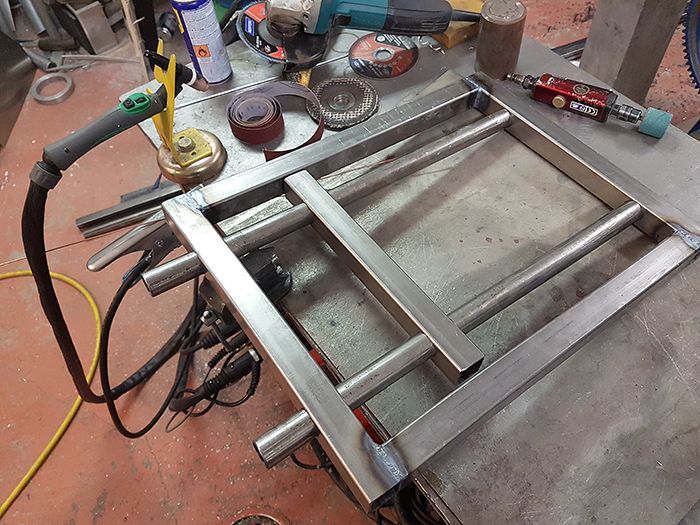
Four engine mounts have been made from stainless angle iron and nylon feets have been milled that will sit on top of the frame tubes.
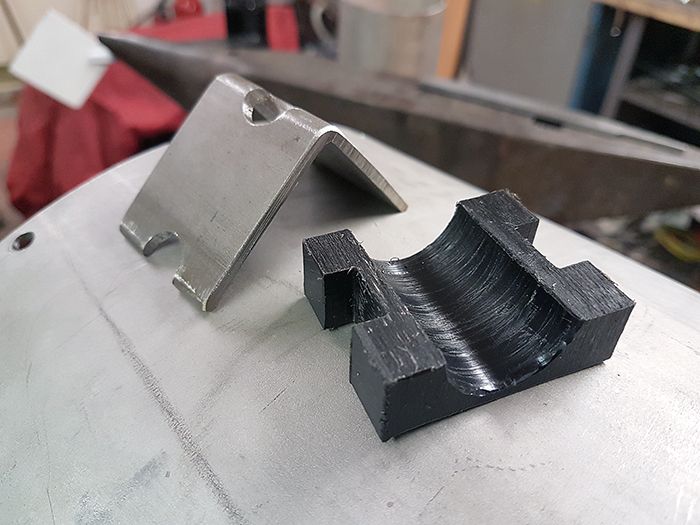
Time to weld the engine mounts in place!
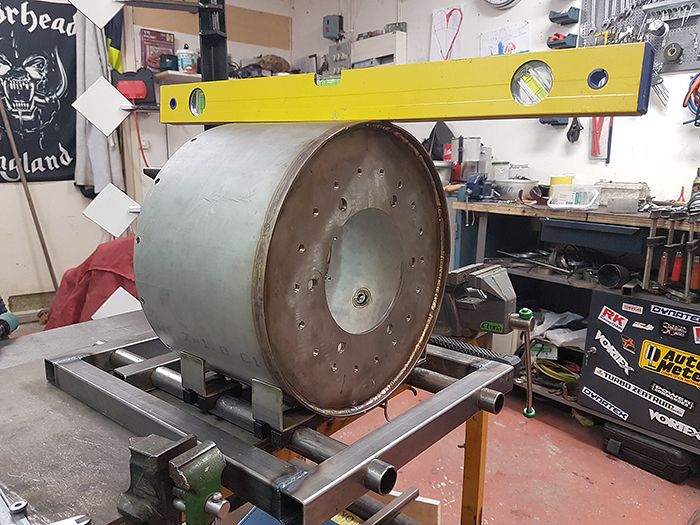
I didn´t weld more than needed to avoid heat distortion of the engine cover.
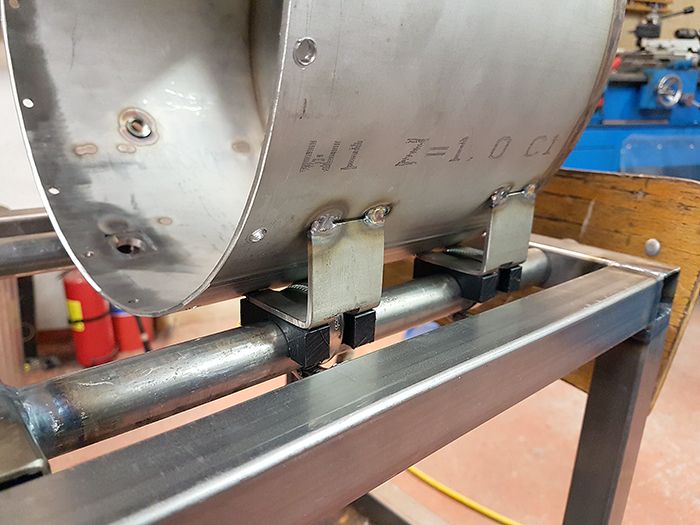
The finished test rig (except for the load cell) with the engine cover fitted, I am planning to mount it to the large fan I will build a motorcycle dyno bench from later. It weighs close to a ton so the engine won´t move it.

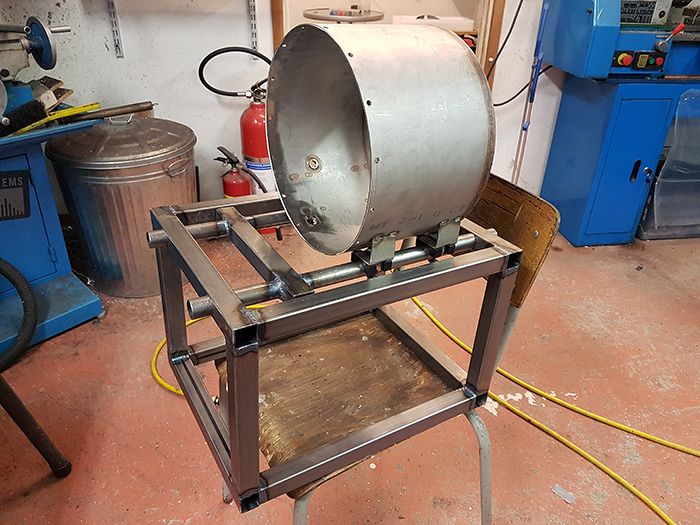
Before calling it a night I wire locked the flame tube screws, no risk that they will fall out now.
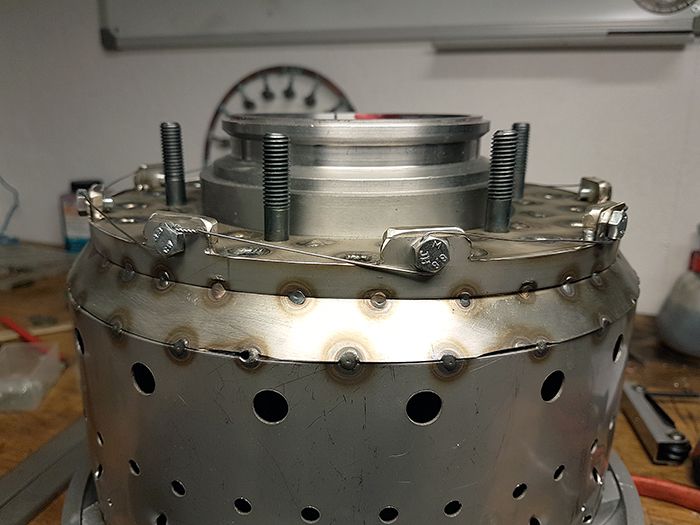
Cheers!
/Anders