As I might have said before I will make an external fuel supply on JU-02 compared to the internal "standard" soldered syringe fuel ring I used on JU-01, it is easy to make but in order to check it for syringe blockage I have to tear down the entire engine which isn´t very practical at a race weekend.
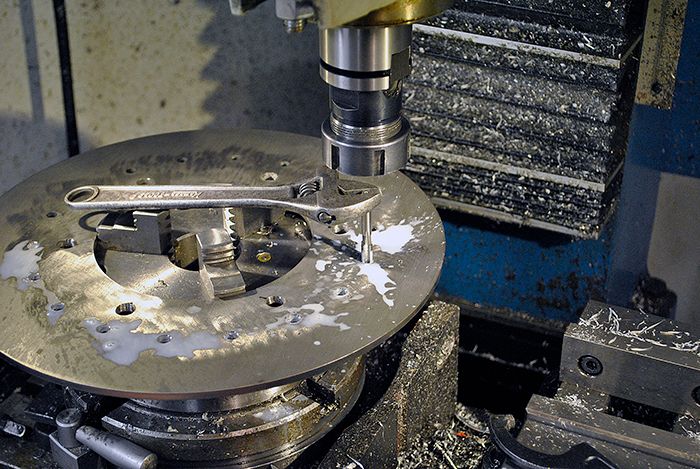
The solution is to complicate things a bit and make an external fuel supply, 18 separate syringe injectors will be fitted in banjo bolts and fitted through threaded holes in the engine cover rear wall pointing into the evaporator tubes. The banjo fittings will be shortened and silver soldered to a length of copper tube and then into a larger diameter circular plenum tube into which the fuel is fed from the pump.
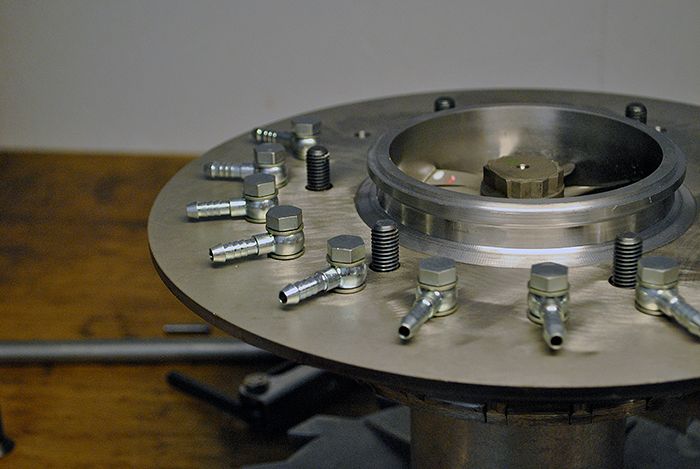
The injectors are made from turned down 3D printer nozzles threaded into the banjo bolt and drilled to accept a 0.7mm syringe needle that is silver soldered in place. This way I can take the injector apart for ultra sound cleaning during overhaul.
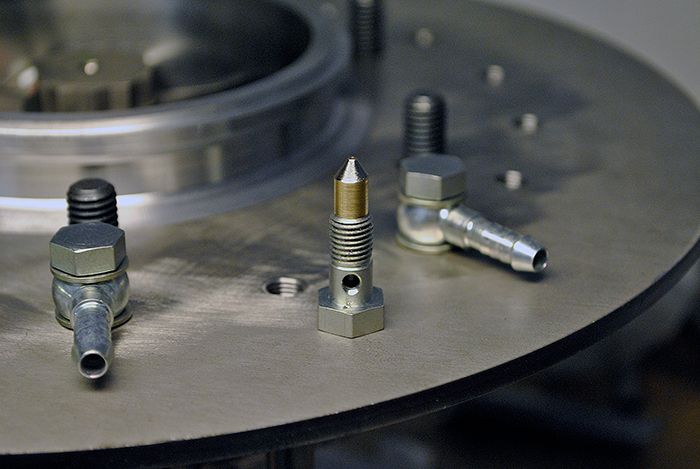
Here below is a picture of how the injectors will line up with the evaporators, the syringe needle will protrude into the bellmouthed entry of the evaporator and have a bend at the end so the kerosene hits the tube wall.
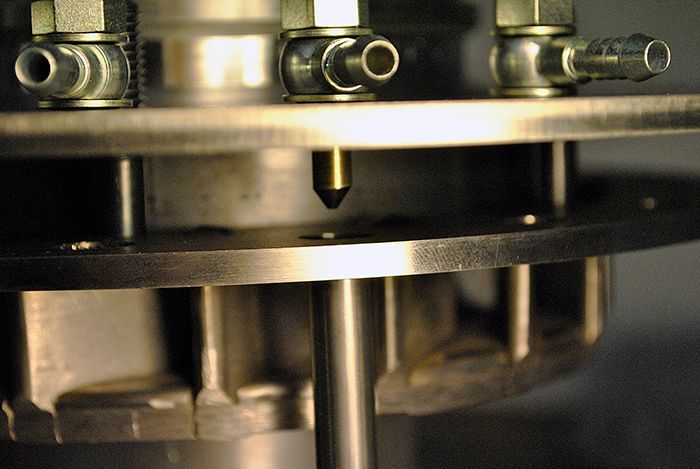
Cheers!
/Anders